BREMBO SVILUPPA ULTERIORMENTE GLI IMPIANTI FRENANTI PER IL CAMPIONATO DEL MONDO DI FORMULA UNO
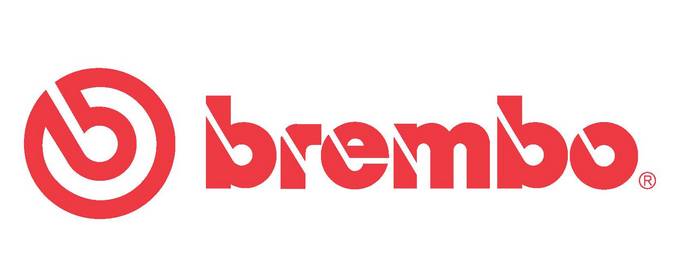
L’azienda italiana si concentra sulla fornitura di impianti frenanti più leggeri, compatti e con prestazioni ottimizzate in termini di raffreddamento e resistenza alle sollecitazioni
Presente in Formula Uno dal 1975, anche per la stagione 2016 Brembo rafforza la propria leadership tecnologica nella massima serie degli sport automobilistici fornendo i propri impianti frenanti ai più importanti team che partecipano al Campionato. Brembo supporta in termini d’innovazione tecnologica, massima affidabilità e soluzioni integrate l’attività di sviluppo di ogni singola squadra, concentrandosi sul lavoro di affinamento dei singoli elementi che compongono gli impianti frenanti, resi più leggeri, più compatti e in grado di garantire un ulteriore miglioramento in termini di prestazioni. Dal punto di vista regolamentare la stagione 2016 di Formula Uno non presenta sostanziali cambiamenti rispetto al 2015, in vista delle importanti evoluzioni tecniche previste nel 2017, che vedranno l’Azienda italiana pronta a raccogliere la nuova sfida tecnologica, con vetture più performanti e capaci di sviluppare maggiori coppie frenanti. A tal proposito, molto lavoro è già stato svolto durante l’inverno dai tecnici Brembo per rendere i dischi freno molto più efficienti e robusti grazie allo spessore maggiorato (nel 2017 si passerà dagli attuali 28mm a 32mm), che consentirà un’ulteriore evoluzione del sistema di raffreddamento degli impianti e la possibilità di contemplare un numero maggiore di fori di ventilazione, rispetto agli oltre 1.200 attuali. La Formula Uno richiede una profonda personalizzazione degli impianti frenanti legati alle diverse scelte progettuali delle singole monoposto. Ciascuno dei team forniti da Brembo richiede un sistema frenante sempre più “su misura”, strettamente integrato con il design della monoposto e soggetto ad uno sviluppo continuo nel corso della stagione. Per quanto riguarda le pinze freno ad esempio, la perfetta integrazione del componente con il sistema di raffreddamento del corner (presa d’aria, drum, deflettori,…) e con le soluzioni aerodinamiche studiate da ogni singolo team, fa sì che ogni componente sia diverso per ogni squadra ed unico. Sono inoltre diverse le scelte legate alla massima ricerca di rigidezza, o al minor peso possibile, spesso decise in funzione delle preferenze dei propri piloti. Oltre alla progettazione dell’impianto frenante, Brembo prosegue il lavoro di sviluppo dei singoli componenti del sistema Brake By Wire. Gli ingegneri hanno ulteriormente ampliato le proprie competenze, producendo diverse componenti del BBW in base alle richieste dei singoli Clienti e lavorando ulteriormente sull’installazione e miniaturizzazione delle stesse. Per alcuni team sono stati sviluppati unicamente alcuni componenti del BBW; mentre per altri è stato svolto un lavoro più ampio che riguarda l’intero circuito: dal simulatore su cui agisce la pompa freno posteriore, all’attuatore comandato dalla centralina e che aziona le pinze al retrotreno, al sistema di valvole di sicurezza che controlla la commutazione. Livello massimo di ventilazione per i dischi freno La ventilazione dei dischi freno Brembo ha subito una costante trasformazione nel corso degli anni, aumentando considerevolmente le prestazioni assolute dell’impianto frenante. Il lavoro di ottimizzazione sul sistema di raffreddamento dei dischi freno, che in Formula Uno possono raggiungere la temperatura massima di oltre 1.000°C, e l’estremizzazione del disegno dei fori di ventilazione, aumentati nel numero assoluto (attualmente oltre i 1.200 per ciascun disco), ha comportato un enorme lavoro di modellazione e simulazione del materiale composito per assicurare sempre la resistenza strutturale pur con lavorazioni così estreme. Tale evoluzione nel design ha comportato anche lo sviluppo di un processo specifico per la lavorazione meccanica che richiede la massima precisione su fori di diametro estremamente ridotto.
Diminuzione notevole del livello di usura del sistema frenante grazie al CER Durante l’inverno i tecnici hanno lavorato sul materiale in carbonio CER del disco freno per migliorare la continuità prestazionale e il range di utilizzo. Il CER ha ridotto in maniera significativa l’usura e, garantendo una più efficace conducibilità termica, offre ridotti tempi di warm-up, massima rapidità nel raggiungimento dell’attrito ottimale, ampio range di utilizzo, sia in termini di pressione sia di temperatura, e una risposta in attrito molto lineare. Tutte caratteristiche che consentono al pilota la perfetta modulazione dell’impianto frenante. L’usura incredibilmente bassa permette inoltre di mantenere le prestazioni inalterate e ripetibili da inizio a fine gara. Nella stagione 2016 il materiale dei dischi freno, CER300, è uguale per tutti i team forniti da Brembo, che prosegue nel lavoro di sviluppo, allo scopo di rendere i propri compositi sempre più performanti. Profondamente personalizzate sono invece le geometrie di ventilazione dei dischi per ogni specifico team. Il kilometraggio di pista consigliato da Brembo per l’utilizzo dei dischi, in ragione dei design estremi oggi raggiunti, è di 800 km in condizioni di temperatura ottimali. Tutti i team hanno a disposizione pastiglie CCR 700 con fino a 80 fori di ventilazione per pastiglia. Anche i fori di ventilazione delle pastiglie sono personalizzati in base alle richieste di ciascun team. Dati significativi In una stagione completa Brembo fornisce mediamente a ciascun team, composto da 2 vetture, il seguente materiale: · 10 set di pinze · Da 140 a 240 dischi · Da 280 a 480 pastiglie Per la produzione di ognuna delle pinze freno in alluminio/litio sono necessarie più di 14 ore consecutive di lavorazione meccanica per raggiungere il miglior bilanciamento possibile tra peso e rigidezza. Brembo consiglia la revisione delle pinze freno dopo 2.500 km di normale utilizzo. Per la produzione e lavorazione meccanica di un disco freno sono necessari 9 mesi. La struttura di Brembo Racing conta su più di cento tecnici specialisti per le varie fasi di simulazione, calcolo, progettazione, industrializzazione e testing. Uno staff di ingegneri di pista è poi a disposizione dei team per tutte le attività di prove e gara.